公司新闻
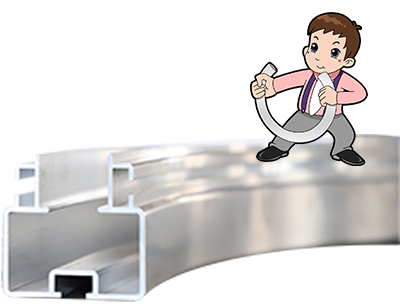
北京拉弯厂摘要:轨道车辆车体如弯梁、侧柱、门扣柱等结构件,尺寸大,精度要求高,一般采用拉弯成形工艺进行加工。北京型材拉弯网介绍了拉弯成形工艺的原理和特点,详细阐述了轨道车辆车体结构件拉弯成形工艺的工艺流程和关键技术,并通过实例分析了拉弯成形工艺在轨道车辆车体结构件加工中的应用效果。研究结果表明,拉弯成形工艺具有成形精度高、表面质量好、生产效率高等优点,能够满足轨道车辆车体结构件的加工要求。
北京盛达伟业型材拉弯厂的关键词:轨道车辆;车体结构件;拉弯成形工艺
**一、引言**
随着轨道交通的快速发展,轨道车辆的安全性和舒适性越来越受到人们的关注。轨道车辆车体结构件作为轨道车辆的重要组成部分,其质量和性能直接影响着轨道车辆的安全性和舒适性。因此,如何提高轨道车辆车体结构件的加工质量和效率,成为了轨道车辆制造企业面临的重要问题。
拉弯成形工艺是一种先进的金属塑性成形工艺,具有成形精度高、表面质量好、生产效率高等优点,被广泛应用于航空航天、汽车、轨道交通等领域。本文将介绍拉弯成形工艺的原理和特点,详细阐述轨道车辆车体结构件拉弯成形工艺的工艺流程和关键技术,并通过实例分析拉弯成形工艺在轨道车辆车体结构件加工中的应用效果。
**二、拉弯成形工艺的原理和特点**
(一)拉弯成形工艺的原理
拉弯成形工艺是将金属板材或管材通过拉伸和弯曲的方式成形为所需形状的一种工艺。在拉弯成形过程中,金属板材或管材首先被拉伸到一定的长度,然后通过弯曲模具将其弯曲成所需的形状。拉弯成形工艺的原理如图 1 所示。
(二)拉弯成形工艺的特点
1. 成形精度高
拉弯成形工艺可以通过精确控制拉伸和弯曲的参数,实现对金属板材或管材的高精度成形。与传统的冲压成形工艺相比,拉弯成形工艺可以减少模具的数量和成本,提高生产效率和产品质量。
2. 表面质量好
拉弯成形工艺可以通过控制拉伸和弯曲的速度和力度,避免金属板材或管材表面出现裂纹、褶皱等缺陷,从而提高产品的表面质量。
3. 生产效率高
拉弯成形工艺可以通过自动化生产线实现对金属板材或管材的连续加工,提高生产效率和降低生产成本。
4. 适用范围广
拉弯成形工艺可以适用于各种金属板材或管材的成形,如铝合金、不锈钢、钛合金等,具有广泛的应用前景。
**三、轨道车辆车体结构件拉弯成形工艺的工艺流程和关键技术**
(一)工艺流程
轨道车辆车体结构件拉弯成形工艺的工艺流程主要包括以下几个步骤:
1. 原材料准备
根据产品设计要求,选择合适的金属板材或管材作为原材料,并进行切割、冲孔等预处理。
2. 模具设计与制造
根据产品设计要求,设计并制造拉弯成形模具。模具的设计和制造质量直接影响着产品的成形精度和表面质量。
3. 拉弯成形
将预处理后的金属板材或管材放入拉弯成形模具中,通过拉伸和弯曲的方式将其成形为所需形状。在拉弯成形过程中,需要控制拉伸和弯曲的速度和力度,避免金属板材或管材表面出现裂纹、褶皱等缺陷。
4. 后续处理
拉弯成形后的产品需要进行后续处理,如切割、焊接、表面处理等,以满足产品的设计要求。
(二)关键技术
1. 模具设计与制造技术
模具设计与制造技术是轨道车辆车体结构件拉弯成形工艺的关键技术之一。模具的设计和制造质量直接影响着产品的成形精度和表面质量。在模具设计过程中,需要考虑产品的形状、尺寸、精度要求等因素,并选择合适的模具材料和制造工艺。在模具制造过程中,需要严格控制模具的加工精度和表面质量,确保模具的使用寿命和可靠性。
2. 拉弯成形工艺参数控制技术
拉弯成形工艺参数控制技术是轨道车辆车体结构件拉弯成形工艺的关键技术之一。在拉弯成形过程中,需要控制拉伸和弯曲的速度和力度,避免金属板材或管材表面出现裂纹、褶皱等缺陷。同时,还需要控制模具的温度和润滑条件,以提高产品的成形精度和表面质量。
3. 材料选择与预处理技术
材料选择与预处理技术是轨道车辆车体结构件拉弯成形工艺的关键技术之一。在选择材料时,需要考虑产品的使用环境、力学性能要求等因素,并选择合适的材料。在材料预处理过程中,需要进行切割、冲孔、清洗等处理,以提高材料的表面质量和加工性能。
**四、实例分析**
以某轨道车辆车体弯梁为例,介绍拉弯成形工艺在轨道车辆车体结构件加工中的应用效果。
(一)产品设计要求
该轨道车辆车体弯梁的形状为弧形,长度为 2000mm,宽度为 300mm,厚度为 3mm,材料为铝合金。产品的设计要求如下:
1. 成形精度:±0.5mm。
2. 表面质量:无裂纹、褶皱等缺陷。
3. 力学性能:屈服强度≥200MPa,抗拉强度≥300MPa。
(二)工艺流程
根据产品设计要求,制定了以下工艺流程:
1. 原材料准备
选择厚度为 3mm 的铝合金板材作为原材料,并进行切割、冲孔等预处理。
2. 模具设计与制造
根据产品设计要求,设计并制造拉弯成形模具。模具的材料为 Cr12MoV,硬度为 HRC58-62。
3. 拉弯成形
将预处理后的铝合金板材放入拉弯成形模具中,通过拉伸和弯曲的方式将其成形为所需形状。在拉弯成形过程中,控制拉伸速度为 10mm/min,弯曲速度为 5mm/min,拉伸力为 100kN,弯曲力为 50kN。
4. 后续处理
拉弯成形后的产品进行切割、焊接、表面处理等后续处理,以满足产品的设计要求。
(三)关键技术
1. 模具设计与制造技术
在模具设计过程中,采用了有限元分析软件对模具的结构进行了优化设计,确保模具的强度和刚度满足要求。在模具制造过程中,采用了高精度数控加工设备对模具进行加工,确保模具的加工精度和表面质量满足要求。
2. 拉弯成形工艺参数控制技术
在拉弯成形过程中,通过实时监测拉伸力和弯曲力的变化,调整拉伸速度和弯曲速度,确保产品的成形精度和表面质量满足要求。同时,还通过控制模具的温度和润滑条件,提高产品的成形精度和表面质量。
3. 材料选择与预处理技术
在选择材料时,选择了具有良好力学性能和加工性能的铝合金板材。在材料预处理过程中,进行了切割、冲孔、清洗等处理,提高了材料的表面质量和加工性能。
(四)应用效果
通过采用拉弯成形工艺,成功地加工出了符合设计要求的轨道车辆车体弯梁。产品的成形精度达到了±0.5mm,表面质量无裂纹、褶皱等缺陷,力学性能满足设计要求。与传统的冲压成形工艺相比,拉弯成形工艺具有成形精度高、表面质量好、生产效率高等优点,能够满足轨道车辆车体结构件的加工要求。
**五、北京拉弯厂结论**
北京型材拉弯网介绍了拉弯成形工艺的原理和特点,详细阐述了轨道车辆车体结构件拉弯成形工艺的工艺流程和关键技术,并通过实例分析了拉弯成形工艺在轨道车辆车体结构件加工中的应用效果。研究结果表明,拉弯成形工艺具有成形精度高、表面质量好、生产效率高等优点,能够满足轨道车辆车体结构件的加工要求。在未来的研究中,还需要进一步优化拉弯成形工艺的参数和工艺流程,提高产品的质量和性能,为轨道车辆制造企业提供更加先进的加工技术。